May 14th, 2020
Manufacture Smarter: Planning for profitability in the post-pandemic period
While the many changes and disruptions that came from the COVID-19 pandemic were not expected as we entered 2020, leaders in all industries have worked hard to restore our nation’s prominence and success as the world continues to respond and recover.
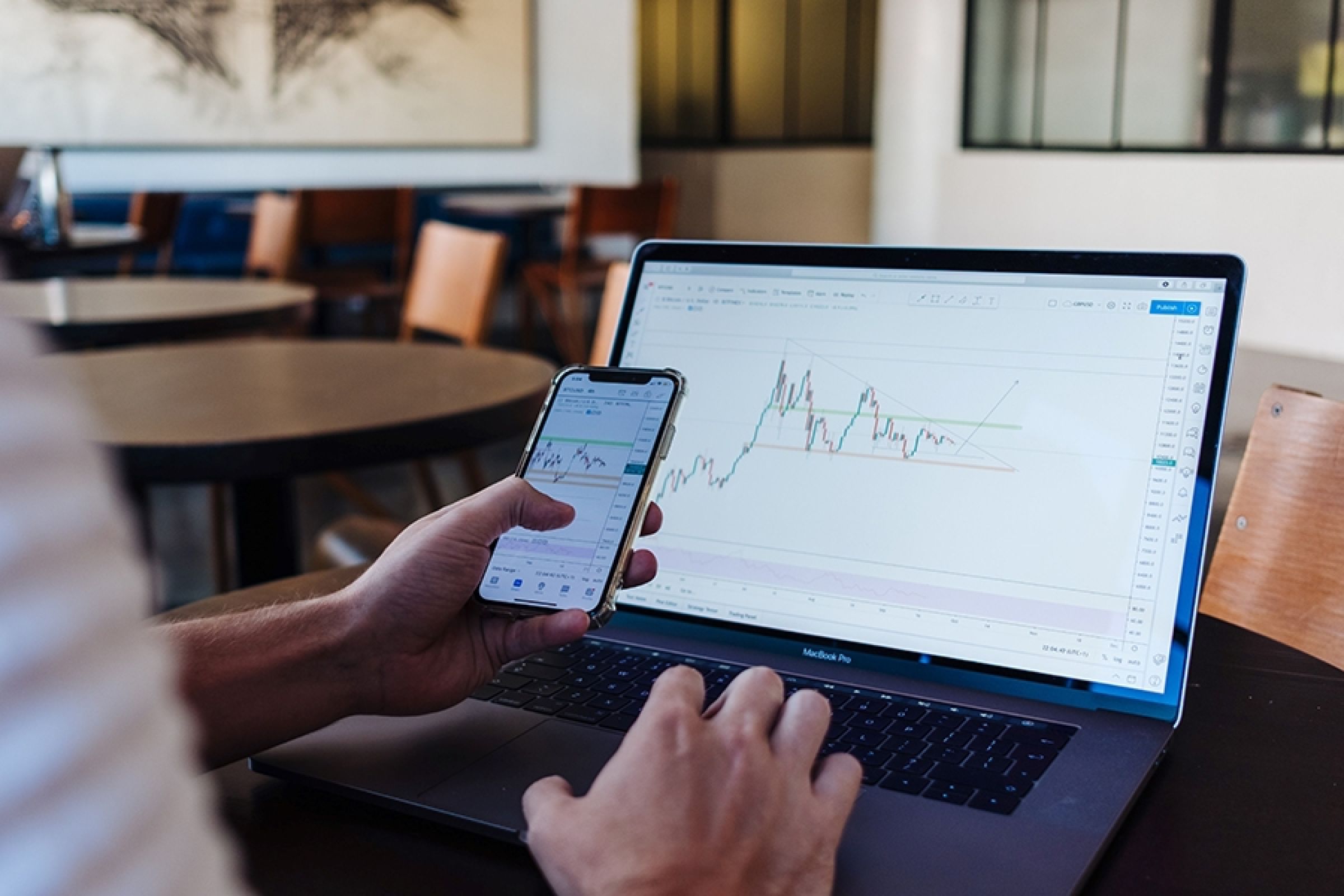
While the many changes and disruptions that came from the COVID-19 pandemic were not expected as we entered 2020, leaders in all industries have worked hard to restore our nation’s prominence and success as the world continues to respond and recover. So, how does this impact the business activities of small and medium-sized manufacturers?
This is a critical time for many as they evaluate how to restore business processes to a profitable level, all while facing the effects of an economy in turmoil. The process of returning to some form of normalcy will be incremental as business leaders must scale their start-up activities with demand-based thinking.
At the same time, thought must be given to how to protect the workforce in the workspace. Business leaders are moving forward into uncharted territory. It is not just a matter of providing personal protective equipment (PPE) and making work assignments to make product. At minimum, there are two paths to consider:
- People: Verify that the workforce, regardless of role in the organization, is prepared medically and psychologically to return to work. Consider these questions:
- Is there a plan to conduct a health evaluation such as a temperature check at the door?
- Since the quarantine period has been lengthy, did anyone experience a family loss?
- Are protocols adequately defined to the level of clarity that may be needed to assure your employees they are in a safe place?
- Process: Reevaluate customer demand to determine whether your future state is appropriate. This may require direct calls to your customer and supplier base to gather facts and scale your business to the new levels of demand.
While you must give every consideration to providing a safe and healthy workplace for your production teams, it also is imperative that leaders consider the demand of customers as they work to restore their processes. The resulting thoughts and efforts should be flexible and adaptable to ensure the organization can remain profitable through any potential unstable periods of demand.
ENSURE YOUR COMPANY IS STRONG & ADAPTABLE WITH LEAN
During this process of restoration, Lean manufacturing practices are the most effective and profitable means to regain the momentum of the business. In our Lean training offerings at The Center, we often discuss “Lean thinking” to show leaders how to develop their processes to be flexible and adaptable to demand, as mentioned above. Several inexpensive Lean tools can be applied to ensure your company is prepared for productive scaling of business to customer demand, including:
- Takt Time Analysis. Takt time is the maximum acceptable time to meet the demands of the customer. In other words, it is the speed with which the product needs to be created to satisfy the needs of the customer. To calculate this, divide the “Net Time Available for Production” by “Customer’s Daily Demand.”
- Cycle Time. This involves the total time from the beginning to the end of your process, as defined by you and your customer. This includes process time, during which a unit is acted upon to bring it closer to an output, and delay time, during which a unit of work is spent waiting to take the next action.
- Waste Identification. In Lean manufacturing, “waste” is any expense or effort that is expended but does not transform raw materials into an item the customer is willing to pay for. The eight types of waste that can be identified and eliminated are defects, overproduction, waiting, non-utilized talent, transportation, inventory, motion and extra processing. By optimizing process steps and eliminating waste, only true value is added at each phase of production.
- Line Balance. Line balancing is a production strategy that involves balancing operator and machine time to match the production rate to the takt time. In other words, the quantities of workers and machines assigned to each task in the line should be rebalanced to meet the optimal production rate.
With assistance from our team at The Center, a targeted plan using these Lean tools can be made to position your company for successful re-entry into the workforce. Learn how here.
The post-pandemic period will be a new learning opportunity for many as we rise to the challenges of restoring the U.S. economy. It is up to the leaders of small and medium-sized manufacturing organizations to give direction through this uncharted territory. If you find that assistance is needed, The Center’s trusted advisors are prepared to ensure you emerge successful. Learn more about how The Center can support your company’s response efforts here.